PM-CNC Gussbearbeitung in Prettin PM-CNC Gussbearbeitung in Prettin: Umstellung sichert Zukunft
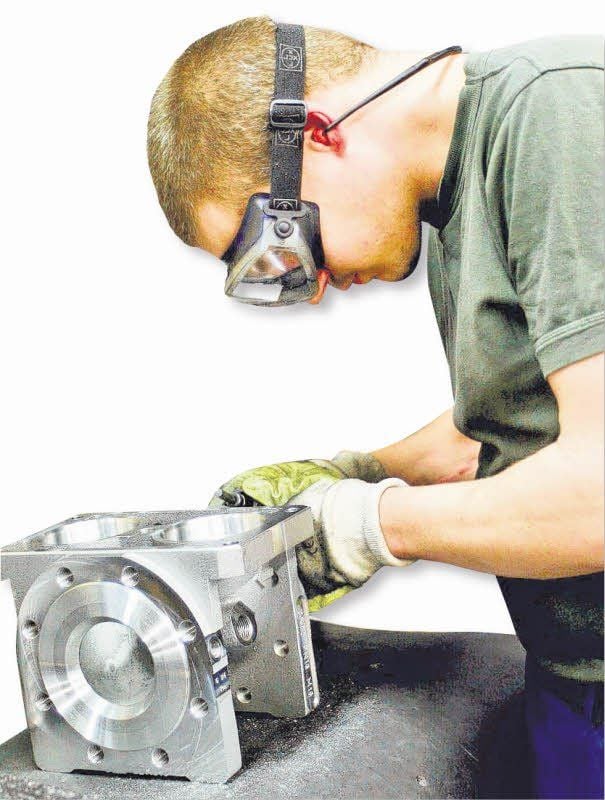
Prettin - „Wir haben uns von einem Auto-Zulieferer zu einem unabhängigen Lohnfertiger entwickelt.“ Roland Görmer, geschäftsführender Gesellschafter der PM-CNC Gussbearbeitung GmbH Am Güterbahnhof 8 in Prettin, ist „seit 20 Jahren dabei“, wie er sagt. Auch wenn es den Betrieb in seiner heutigen Ausprägung erst seit 1997 gibt. Und der Diplom-Ingenieur klingt nicht unzufrieden. Immerhin werden - was wohl nicht einmal den Prettinern bekannt ist - jährlich gut 5 000 Tonnen Gussteile in dem Unternehmen mit 50 Beschäftigten umgeschlagen. Im November 2015 waren es zum Beispiel rund 500 Tonnen. Es handelt sich, um den großen Rahmen abzustecken, vor allem um Produkte für die Fahrzeug- und Verkehrstechnik sowie die Gas- und Öl-Industrie und Offshore-Anlagen.
Nach den einzelnen betrieblichen Stationen beziehungsweise Fertigungsschritten gefragt, die ein Werkstück bei der PM-CNC Gussbearbeitung GmbH in Prettin durchläuft, gibt Roland Görmer folgende Beschreibung: Am Anfang jedes Wertschöpfungsprozesses steht ein Guss-Rohling. Der wird im Auftrag des betreffenden Kunden und nach dessen konkreten Vorgaben bei einer entsprechenden Gießerei bestellt.
In den Werkshallen des Prettiner Betriebes erfolgt dann die mechanische Bearbeitung des Rohlings laut vorgegebener Zeichnung bis zum geforderten Lieferzustand. In einer sehr hohen Genauigkeit (im Tausendstel-Millimeter-Bereich) wird gedreht, gefräst, gebohrt; Gewindeschneiden gehört im weiteren ebenso zu den Arbeitsgängen wie das Herstellen von Passungen (bezieht sich auf zwei gepaarte, toleranzbehaftete Teile mit gleichem Nennmaß).
Anschließend muss das so bearbeitete Gussteil noch entgratet werden. Es folgen - je nach Kundenwunsch - eine Festigkeits- und Dichtheitsprüfung, eine Pulverbeschichtung oder eine Nasslackierung. Zum Schluss geht es ans Verpacken des Werkstücks, auch dabei gilt es, die Vorgaben des Kunden zu beachten.
Als Beigabe werden dem jeweiligen Teil beim Verpacken die entsprechenden Zertifikate zugeordnet. „Das ist eine Frage der Qualitätssicherung“, bemerkt Geschäftsführer Roland Görmer dazu und hängt die Messlatte sehr hoch: „Jeder Mitarbeiter muss da 100 Prozent bringen.“
Dafür steht das Prettiner Unternehmen mit seinem Namen. Der setzt sich zusammen aus PM für Precision Manufacturing (Präzisionsfertigung) und CNC für Computerized Numerical Control (rechnergestützte numerische Steuerung), was ein elektronisches Verfahren zur Steuerung von Werkzeugmaschinen ist.
Als entscheidende Wegmarke der bisherigen Erfolgsgeschichte sieht der Geschäftsführer, dass 2006 ein flexibles Fertigungssystem eingeführt wurde. Es besteht aus einer Kombination von modernen hochkomplexen CNC-Werkzeugmaschinen des Herstellers Okuma (Japan) und einem ebensolchen Regallagersystem des Anbieters Fastems (Finnland).
Motor der ganzen Firma
Für den Anfang legte sich das Prettiner Unternehmen zwei Okuma-Werkzeugmaschinen zu. 2014 kam als eine der jüngeren Investitionen die dritte hinzu. „In Ostdeutschland ist diese Konstellation mit Fastems- und Okuma-Technik wohl einmalig“, schätzt Roland Görmer ein. Und: „Diese flexible Fertigung war und ist der Motor für die gesamte Firma. Wir konnten dadurch Kunden gewinnen, die sehr hohe Ansprüche stellen.“ Was sich auf die Qualität ebenso beziehe wie auf die Kunden- und Termintreue. „Die Entscheidung zu der Flexibilisierung ist bereits 2005 gefallen, sie hat den Bestand des Betriebs gesichert. Sonst würde es die Firma PM-CNC heute wohl schon nicht mehr geben.“
„Mit dem System Okuma-Fastems sind wir in der Lage, Produkte aus unterschiedlichsten Güssen, egal ob groß oder klein, zu fertigen“, verdeutlicht der Geschäftsführer. 54 Maschinenpaletten seien ständig mit mechanisch zu bearbeitenden Teilen bestückt in dem elektronisch verwalteten Regallager vorhanden und abrufbar. Die CNC-Werkzeugmaschinen, zu denen sie auf Anforderung automatisch transportiert werden, übernehmen dann das Bohren, Fräsen, Gewindeschneiden und Passungen herstellen in beinahe unvorstellbarer Genauigkeit (siehe dazu auch „Produktionskette“). „Jede Maschine hat dafür ein mit 240 Werkzeugen bestücktes Magazin“, sagt der Firmen-Chef, „daher kommt auch die Flexibilität.“ Für alle Bearbeitungsgänge an einem Getriebe- oder Pumpengehäuse benötige man immerhin zwischen 30 und 40 unterschiedliche Werkzeuge.
Mit der Flexibilisierung einher geht auch eine bessere zeitliche Auslastung, wie Roland Görmer darlegt. So funktioniert die PM-CNC Gussbearbeitung GmbH heute als Mischbetrieb: Die normale Fertigung, zu der auch konventionelles Drehen und Fräsen gehören, läuft zweischichtig. Die flexible Fertigung hingegen ist dreischichtig ausgelastet. Hier werden Teile für Eisenbahnen, Gießereibetriebe, für Bremsanlagen, Gehäuse für Kran- und Offshore-Anlagen gefertigt. Wobei es sich wie gesagt immer um Gussteile handelt - die Palette reicht da von Grau- und Aluminiumguss über Rotguss, schmiedeeiserne Teile, Messing und Kupfer biss hin zu Stahlguss. Nur eins findet man in den Werkhallen unweit vom einstigen Prettiner Bahnhof nicht: Plasteteile. Anfang 2015 trat ein wichtiger Kunde an die PM-CNC GmbH mit der Frage heran, ob sie ihr Portfolio noch erweitern möchte.
Unter extremem Druck
Daraufhin wurde in Prettin begonnen, eine Festigkeits-, Dichtheits- und Druckprüfungsanlage aufzubauen. In ihr werden die zu testenden Teile - zum Beispiel Stellgliedgehäuse für die Gas- und Öl-Industrie (auf Förderplattformen und an Pipelines) - Drücken bis 100 bar ausgesetzt. Entsprechend viele Sicherheitsbestimmungen sind einzuhalten und bauliche Vorkehrungen zu treffen. Ab September lief der Probebetrieb. Inzwischen ist das Zertifizierungsverfahren nach Druckprüfungsrichtlinie abgeschlossen. Dieser Tage erwartet Roland Görmer die zugehörige, alles entscheidende Urkunde.
Eine weitere Innovation betrifft eine Teilewaschanlage für Objekte bis 350 Kilogramm. In ihr werden die Gehäuse nach der mechanischen Bearbeitung, einschließlich Nachbehandlung, von Produktionsrückständen befreit und anschließend kalt-phosphatiert, das heißt sie bekommen bei circa 70 Grad Celsius einen dünnen Schutzfilm gegen Korrosion. (mz)
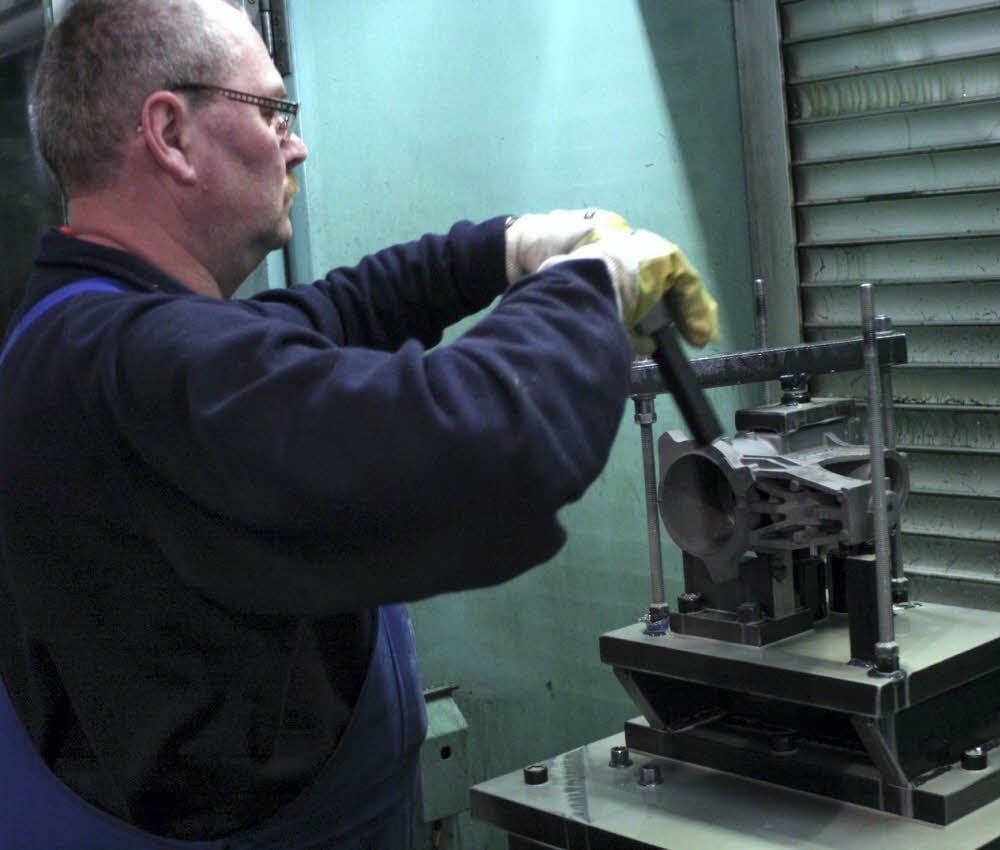