Neue Seidenstraße Elektro-Thermit und neue Seidenstraße: Ammendorfer entwickeln für Bahnstrecken in China und Russland
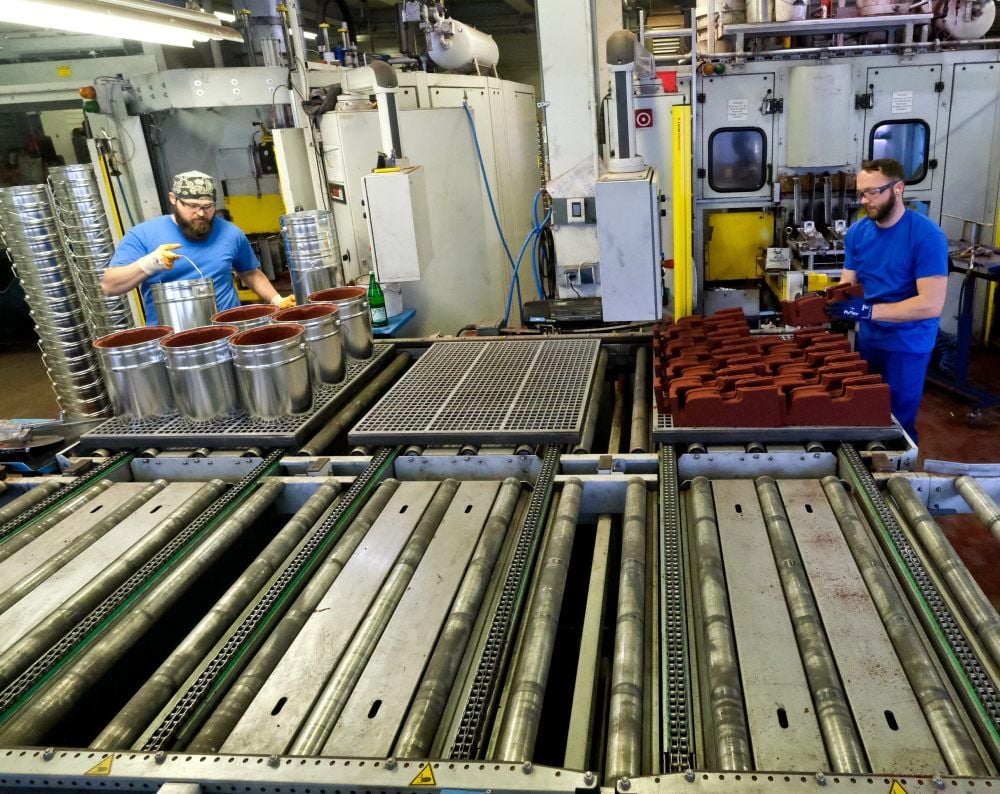
Halle (Saale) - Der Plan ist gigantisch: Zehntausend Kilometer Bahnstrecke sollen Spanien, Frankreich, Deutschland und weiter Polen, Russland und China im Rahmen des Projekts „Neue Seidenstraße“ miteinander verbinden. Damit will China die Versorgung des Landes und den Handel verbessern. Doch um den Plan umzusetzen, braucht es ein Unternehmen aus Halle: die Elektro-Thermit-Werke, die Teil der weltweiten Goldschmidt Smart Rail Solutions-Gruppe ist.
Denn das Ammendorfer Unternehmen ist nach eigenen Angaben Weltmarktführer im lückenlosen Verschweißen von Gleisen mit dem patentierten Thermit-Schweißverfahren, durch das Bahnfahren ohne das früher übliche Klack-Klack-Geräusch möglich ist. Vor allem für Hochgeschwindigkeitsstrecken ist dies von Bedeutung.
„Ein Drittel des Weltverbrauchs für dieses Schweißverfahren wird in Halle produziert“
„Ein Drittel des Weltverbrauchs für dieses Schweißverfahren wird in Halle produziert“, sagt Matthias Wewel, Geschäftsführer der Elektro-Thermit. Schwesterunternehmen in Australien, Südafrika, Nordamerika und Brasilien übernehmen den Rest.
In China, so Wewel, seien die Arbeiten an der „Neuen Seidenstraße“ bereits abgeschlossen. „Jetzt werden in Russland Gleise lückenlos verschweißt“, berichtet er. Die Gleise, die zum Teil noch aus der Zarenzeit stammen, werden erneuert und eben mit dem 120 Jahre alten Patent auf den neuesten Stand der Technik gebracht.
Thermit in Halle: 170 Mitarbeiter in Forschung, Entwicklung, Produktion und Vertrieb
170 Mitarbeiter in Forschung, Entwicklung, Produktion und Vertrieb sorgen am Standort Halle dafür, dass jährlich etwa eine Million Portionen des Aluminium-Eisenoxid-Pulvers produziert werden. Das ist das Kernprodukt für das lückenlose Verschweißen, das im strengen Sinne gar kein Schweißen ist, wie Matthias Wewel erklärt.
„Das Gleis kommt bei dem Verfahren in eine Form aus feuerfesten Material, alles wird auf etwa 1000 Grad vorgewärmt“, sagt er. Dann wird das Thermit-Pulvergemisch in einem Tiegel gezündet, flüssiges Metall läuft so bei etwa 3.000 Grad in die Lücke zwischen den Gleisen. Die Form wird danach abgeschlagen.
Elektro-Thermit: Formen für die unterschiedlichen Gleisprofile
Beides, die Formen für die unterschiedlichen Gleisprofile, und das Pulver, werden seit 1922 in Ammendorf produziert. Im Vorjahr hatte das Unternehmen, das 1919 in Berlin gegründet wurde, sein 100-jähriges Bestehen gefeiert. Immer wieder fällt im Zusammenhang mit Elektro-Thermit der Begriff „hidden champion“ (englisch: heimlicher Gewinner). Gemeint ist damit ein mittelständisches Unternehmen, das mit Spezialprodukten Marktführer ist, ohne das große Teile der Öffentlichkeit es wissen.
Dabei war das Unternehmen an so spektakulären Bauprojekten wie der 14 Kilometer langen Schienentrasse bei Istanbul beteiligt, die seit 2013 Europa und Asien in einem Tunnel unter dem Bosporus verbindet. Hochgeschwindigkeitstrecken in Japan und auch die zwischen Berlin und Erfurt sind Projekte, bei denen das patentierte Thermit-Verfahren angewendet wurde.
Elektro-Thermit: Von 1945 bis 1990 gehörte das Werk zum VEB Ammendorfer Plastwerk
„Vor allem kommt unser Verfahren jedoch beim Wechseln von Weichen, Gleisen und Bögen zum Einsatz“, sagt der Geschäftsführer. Seit 1. März gibt es nun auch den neuen Namen „Goldschmidt smart rail solutions“, unter dessen Dach alle Unternehmen der Gruppe firmieren. „Damit machen wir deutlich, dass auch Service, Messtechnik, Hydraulikwerkzeuge und anderes zu unserem Expertennetzwerk rund um die Schiene gehören“, so Wewel.
Damit hat das Unternehmen in seiner Geschichte einen weiteren Schritt gemacht. Im Jahr 1895 hatte der Berliner Chemiker Hans Goldschmidt das Thermit-Verfahren entdeckt. 1919 gründete er sein Unternehmen, das 1922 auch das Werk in Ammendorf aufkauft.
Von 1945 bis 1990 gehörte das Werk zum VEB Ammendorfer Plastwerk, 1990 kaufte es die Mutterfirma Goldschmidt AG zurück. 2005 verlagerte Elektro-Thermit seinen Sitz von Essen (Nordrhein-Westfalen) wieder nach Halle. Bis heute hat das Unternehmen rund 30 Millionen Euro in den Standort Halle investiert, so Geschäftsführer Wewel. (mz)
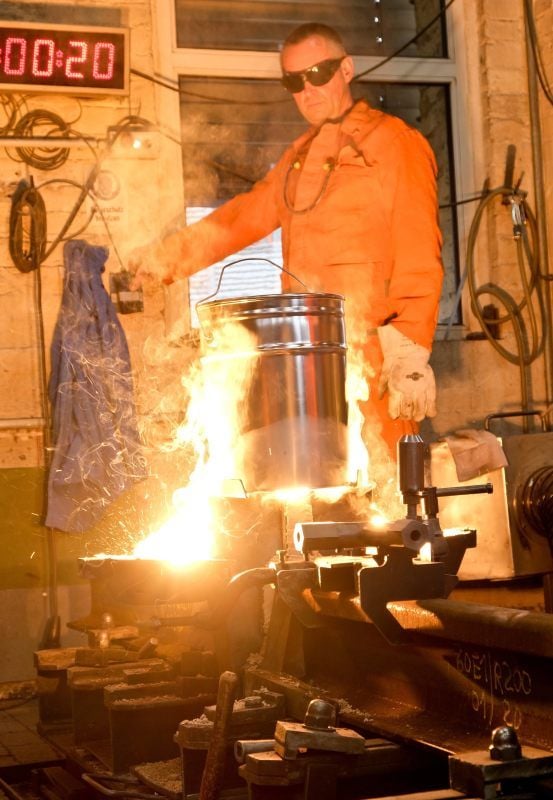
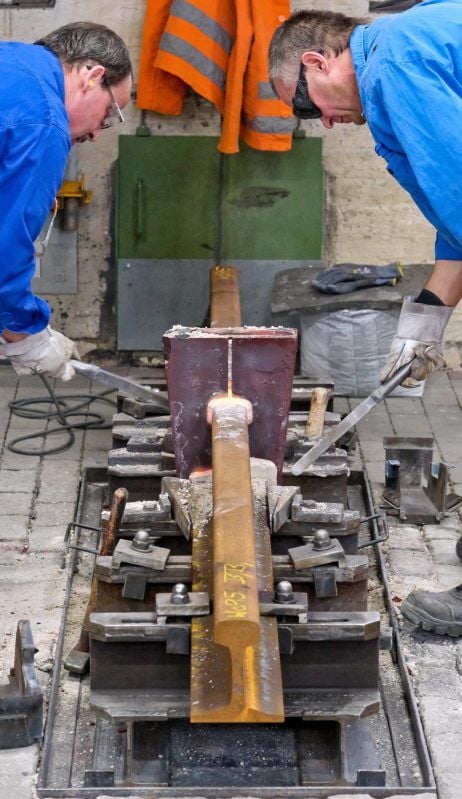
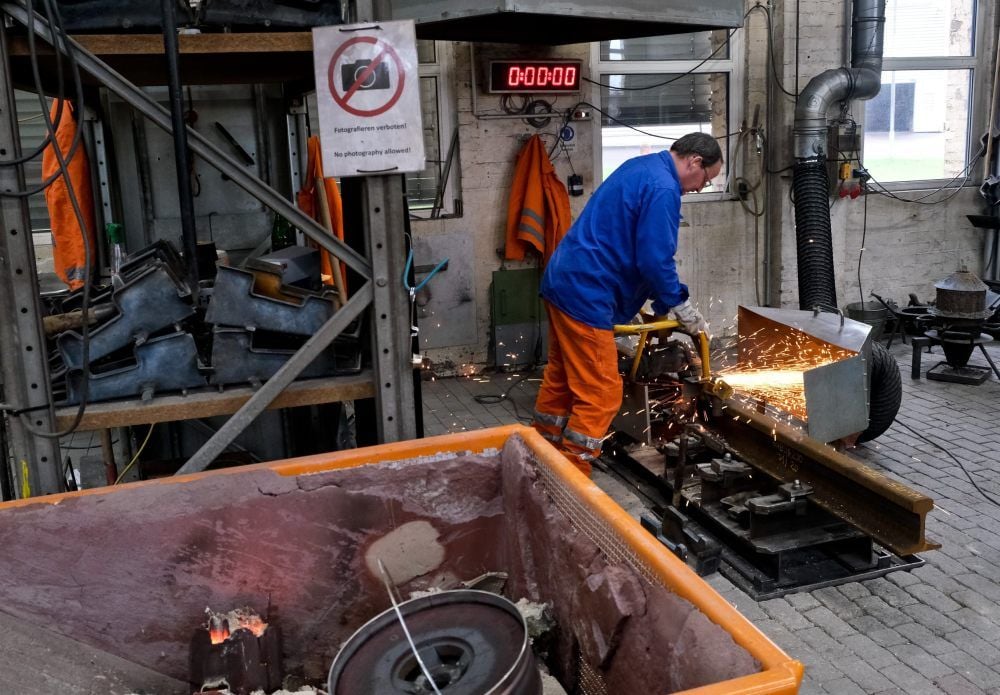