BMW in Leipzig BMW in Leipzig: Werk als beste Fabrik 2013 ausgezeichnet
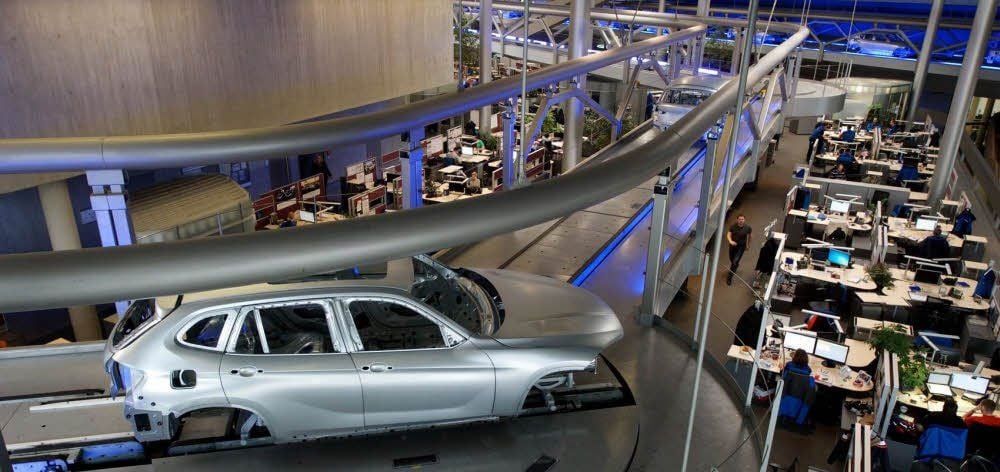
Leipzig/MZ - Wo Menschen arbeiten, passieren Fehler: Gerade in der Automobil-Produktion, in der hunderte Einzelteile zu einem Ganzen gefügt werden, können auch kleine Fehlgriffe großen Schaden anrichten. Qualitätssicherung schreiben sich daher alle Hersteller groß auf die Fahne.
Jeden Morgen sitzen verantwortliche Produktionsmitarbeiter im BMW-Werk in Leipzig zusammen. Die Fertigung des Vortages wird ausgewertet: Wie viele Fehler gab es pro Fahrzeug? Welche Stückzahlen wurden erreicht und in welcher Zeit? „Jeden Tag versuchen wir so, ein Stück besser zu werden“, sagt Hanne Dinkel, Leiterin der Produktionssteuerung. Die Leipziger sind bei dieser Arbeit offensichtlich akribisch und erfolgreich.
Produktion geschieht im Takt
Das Werk hat den Industriewettbewerb „Beste Fabrik 2013“ gewonnen, der von den Managementschulen INSEAD, WHU – Otto Beisheim School of Managemet und der Zeitschrift „Wirtschaftswoche“ verliehen wird.
Ein Beispiel: Um teure Fehlerbehebungen am Ende der Fertigung zu vermeiden, findet die Qualitätskontrolle direkt am Band statt. Die Mitarbeiter überwachen jedem Montageschritt selbst, was - treten Probleme auf - natürlich auch Stress bedeutet. Die Taktzeit für jeden Arbeitsschritt ist mit 76 Sekunden äußerst knapp. BMW hat daher eine „Reißleine“ eingeführt. Bandarbeiter können diese ziehen, wenn sie einen Fehler nicht selbst sofort ausbügeln können. Ein Vorarbeiter hilft dann bei der Behebung des Mangels. „Dieses Hilfssystem sichert hohe Standards und nimmt Druck vom einzelnen Bandarbeiter“, erklärt Betriebsratschef Jens Köhler.
Die Mitarbeiter bei der Optimierung der Produktion einzubeziehen, ist bei BMW keine Marketingfloskel. Nach Angaben von Dinkel werden 11 000 Ideen in gut 160 kleinen Workshops pro Jahr von den Kollegen eingebracht, um die Geschwindigkeit und die Qualität der Produktion zu verbessern. Die Mehrzahl davon werde umgesetzt.
Lohn der Mühe: Nach Angaben von Dinkel ist es so gelungen, die Produktion des kleinen Geländewagens X1 um 20 Prozent zu erhöhen. Vor allem an sogenannten Engpassstellen etwa an Schweißanlagen sei die Fertigung optimiert worden. In der Pannenstatistik des ADAC siegte der X1 zuletzt in der Kategorie „Untere Mittelklasse“.
740 neu produzierte Fahrzeuge der Modellreihen 1er und X1 verlassen täglich das Werk - dies ist die Kapazitätsgrenze. Seit 2009 ist die Produktionszeit laut Harbour Report der Managementberatung Oliver Wyman von 27,1 auf 26,3 Stunden pro Fahrzeug gesunken. Alleine die Zeit fürs Lackieren reduzierte sich bis 2011 um 35 Prozent, die Montage geht um 40 Prozent schneller, schreibt die Wirtschaftswoche. Die Juroren des Industriepreises überzeugte „die Strategieumsetzung bis auf Mitarbeiterebene“ und „vorbildliche Leistungskultur“. Werksleiter Manfred Erlacher lässt mitteilen: „Ich bin sehr stolz auf diesen Preis, den ich stellvertretend für meine Mitarbeiter entgegen nehme.“
Das erst im März 2005 eröffnete Werk wurde von der Star-Architektin Zaha Hadid entworfen. Rohkarosserien laufen für Besucher und Mitarbeiter gut sichtbar durch das Zentralgebäude. Viel bedeutender ist allerdings, dass BMW auf dem Firmengelände auch zahlreiche Zulieferer angesiedelt hat, die bis an die Produktionsstraße liefern. Dies ist nicht unumstritten. Einige Arbeitsprozesse, die in anderen Werken BMW-Mitarbeiter übernehmen, wurden ausgegliedert. Auch so wurde Flexibilität gewonnen und Kosten gespart. Zudem arbeiteten in Leipzig jahrelang viele Leiharbeiter, um Produktionsschwankungen auszugleichen. Zwischenzeitlich waren ein Drittel der derzeit 3.200 festen Beschäftigten Leiharbeiter. Dagegen ging der Betriebsrat vor. Den Arbeitnehmervertretern war dies zu viel.
Zuschlag für Elektroau
Konzern und Betriebsräte einigten sich schließlich friedlich. Nach Worten von Betriebsratschef Köhler wurden bereits 2012 rund 250 Leiharbeiter übernommen, in diesem Jahr sollen weitere 500 folgen.
Derzeit rüstet sich das Werk für die Produktion des neuen Elektrofahrzeuges BMW i3, die noch im Herbst starten soll. 400 Millionen Euro hat BMW dafür investiert. Es entstand ein Werk im Werk. Dass die Sachsen den Zuschlag für die Produktion bekamen, lag nicht nur an frei verfügbaren Flächen und Fördermitteln. Ein ranghoher BMW-Manager sagte zuletzt: „In Leipzig sind viele Prozesse noch nicht so eingefahren. Das Werk kann sich schnell und flexibel auf neue Anforderungen einrichten.“
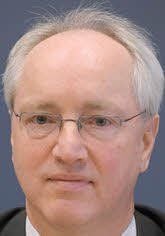